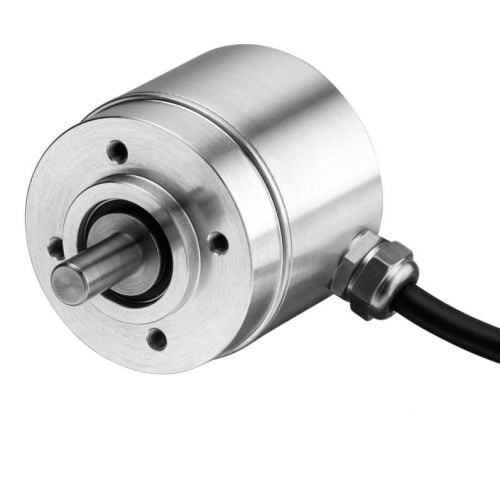
Acuro AC36
The AC36 is an optical absolute rotary encoder with a multi-turn gearbox and optical scanning, size 36 mm. It is fitted with a solid shaft and physically compatible with standard incremental encoders. Thanks to its compact construction, the AC36 can directly replace corresponding incremental encoders. As a result, it is possible to make full use of the technical benefits of absolute encoders in equipment manufacturing and medical engineering, to name but two of the many applications. The mechanical concept is based on a shaft assembly mounted in dual ball-bearings. The AC36 complements the ACURO industry product family while offering the same performance data as the 58 mm variants but with a smaller device size
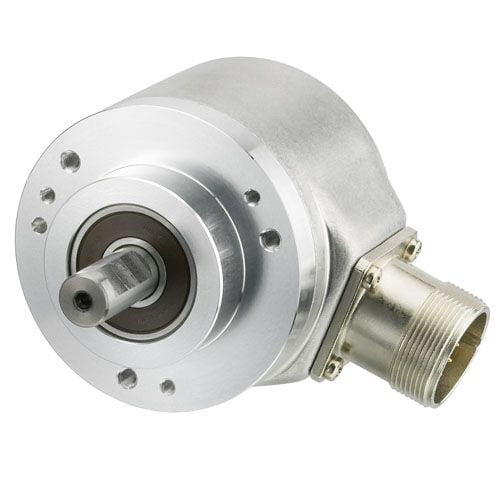
Acuro AC58
The AC58 series comprises a range of absolute rotary encoders with optical scanning for many different application areas. The 58 mm encoders are available in solid shaft and hollow shaft versions and meet the requirements of almost all industrial applications and demanding applications involving motor feedback. In single and multiturn versions, these encoders achieve a resolution of up to 34 bits (22 bits single turn, 12 bits multiturn, depending on the interface). In addition to connections via SSI/BiSS, numerous other interfaces such as EtherCAT, Profinet, Profibus, CANopen, CANlayer2, DeviceNet, Interbus and SUCOnet are available. Click on one of the connection options for the associated data sheet
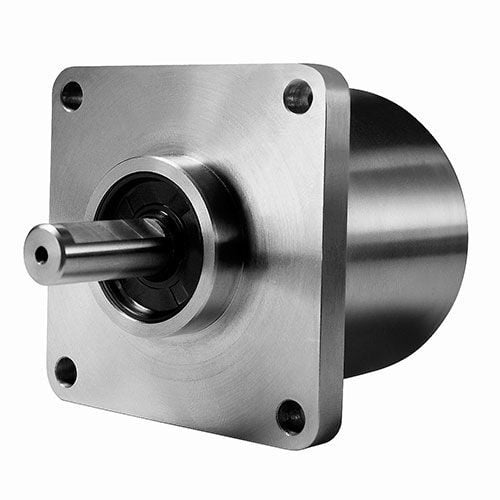
Acuro AC59
The AC59 series combines a series of absolute rotary encoders with optical scanning that have been specially designed for use in extreme ambient conditions. The size 58 mm encoders have a stainless steel housing and are particularly suited to oil and gas applications, marine fittings, the food industry, packaging industry and offshore applications. As single-turn and multi-turn versions, these encoders achieve a resolution of up to 29 bits (17 bits single-turn, 12 bits multi-turn).
Data Sheet BSSI Data Sheet Parallel
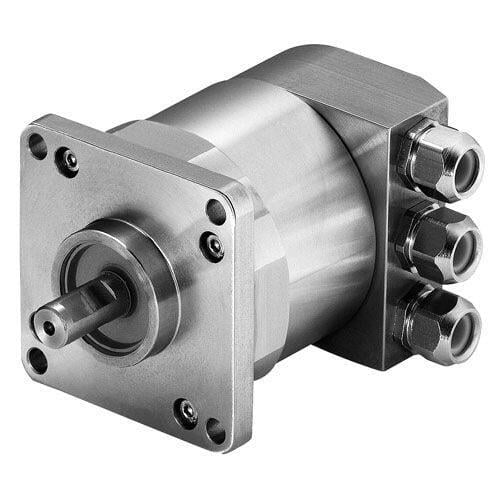
Acuro AC61
The AC61 series combines a series of absolute rotary encoders with optical scanning that have been specially designed for use in extreme ambient conditions. The size 58 mm encoders have a stainless steel housing and are particularly suited to oil and gas applications, marine fittings, the food industry, packaging industry and offshore applications. As single-turn and multi-turn versions, these encoders achieve a resolution of up to 29 bits (17 bits single-turn, 12 bits multi-turn). Connection options are Profinet, Profibus, CANopen, CANlayer2, DeviceNet and Interbus. Click the output for the datasheet
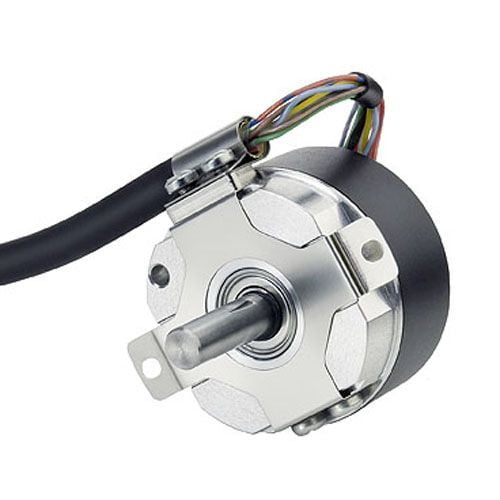
Acuro AD34
The AD 34 is the most compact absolute encoder in its performance class. It is available with a resolution of up to 19 bits single-turn and 12 bits multi-turn. The mechanical concept is based on a shaft assembly mounted in dual ball-bearings with a flexible torque support. Thanks to its innovative shaft assembly system, the AD34 saves time when configuring the motor shaft. Just a simple 6 mm central bore in the "B" end of the motor shaft is sufficient. The notched shaft of the AD34 is press-fitted in the "B" end of the motor shaft in a single operation. The BiSS or SSI communication interface enables control circuits to be set up that are completely digital.
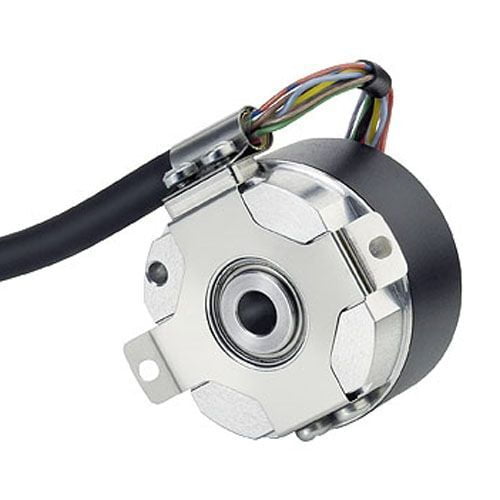
Acuro AD35
In launching the AD35, HENGSTLER has introduced the shortest hollow-shaft encoder in the world. The AD35 is available with a single-sided 8 mm hollow shaft and a single-turn resolution of up to 22 bits. The mechanical concept is based on a shaft assembly mounted in dual ball-bearings with a flexible torque support. The AD35 is suitable for fitting in BLDC servo motors with small frame heights. The BiSS or SSI communication interface enables control circuits to be set up that are completely digital.
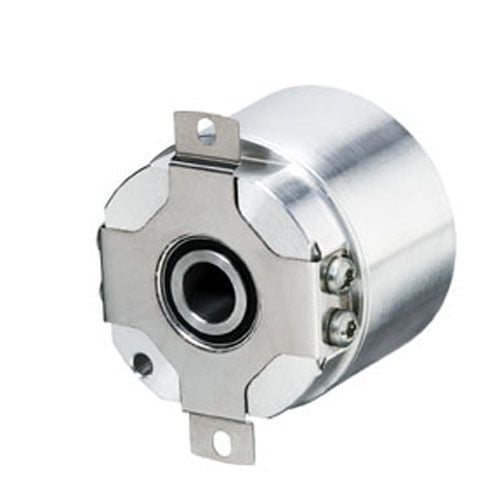
Acuro AD36
The AD 36 is an optical absolute encoder with a multi-turn gear and optical scanning, size 36 mm. As the only model in its class, it offers an 8 mm through hollow shaft, which allows resolver-compatible installation. The mechanical concept is based on a shaft assembly mounted in dual ball-bearings with a flexible torque support. The AD36 is suitable for fitting in BLDC servo motors with small frame heights. The BiSS or SSI communication interface enables control circuits to be set up that are completely digital. It is available with resolutions of up to 19 bits single-turn and 12 bits multi-turn.
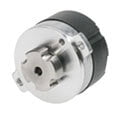
Acuro AD37 Safety
Singleturn and Multiturn Encoder for high performance motion control; Encoder for Functional Safety applications (SIL2 PLd, SIL3 PLe, category 3); Single Cable Solution with ACURO® link interface for 2 and 4 wire applications; Most compact absolute multiturn encoder of its class (Mounting depth: 29 mm); Motor winding temperature sensor input; Resolution: up to 20 Bit ST + 12 Bit MT; Wide operating temperature range (-40°C to +115°C); Up to 12,000 rpm continuous operation; Encoder data stored in “Electronic Data Sheet (EDS)” inside encoder
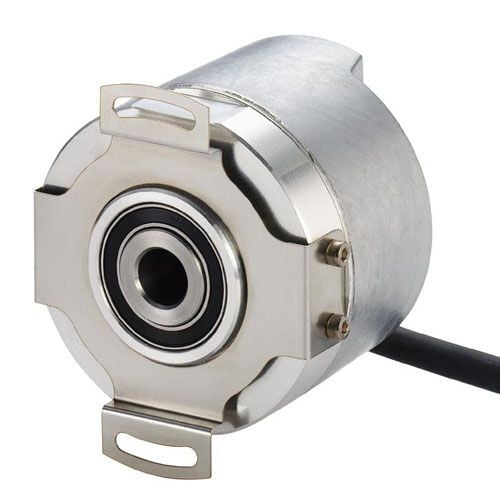
Acuro AD58
The AD58 multi-turn absolute encoder is an optical encoder with a multi-turn gear and optical scanning. The mechanical concept is based on a shaft assembly mounted in dual ball-bearings with a flexible torque support. As a result, these encoders are suitable for incorporating in BLDC servo motors and such demanding applications as CNC, precision positioning and high-resolution printing. The encoder is available with resolutions of up to 22 bits single-turn and 12 bits multi-turn.
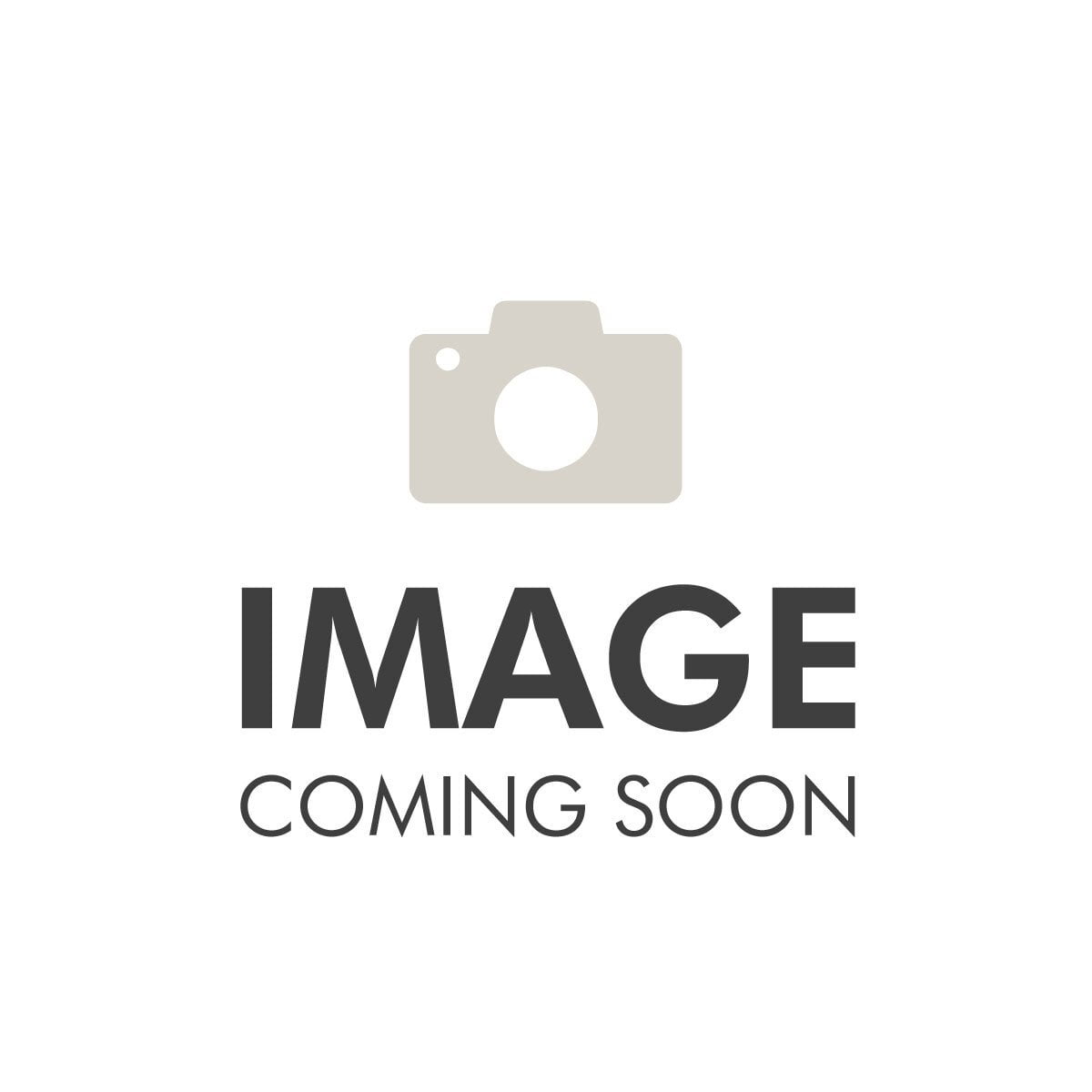
Acuro AD58 Safety
Singleturn and Multiturn Encoder for high performance motion control; Encoder for Functional Safety applications (SIL2 PLd, category 3); Resolution: up to 24 Bit ST + 12 Bit MT; DRIVE-CLiQ interface; ACURO link interface; Wide operating temperature range; Up to 10,000 rpm continuous operation; Motor Temperature Logging and Temperature Monitoring of Encoder; Optical encoder with a true geared multiturn
Data Sheet
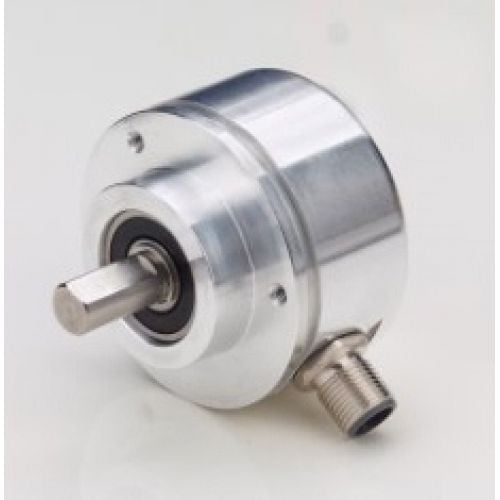
Acuro AR60
Besides the robust magnetic Sensor technology the AR60 offers a wear-free electronic Multiturn which works without the need of a battery. The robust design allows up to 10.000 rpm within a wide temperature range of -40 °C ... +100 °C. SSI, CANopen and Analog interfaces are available.
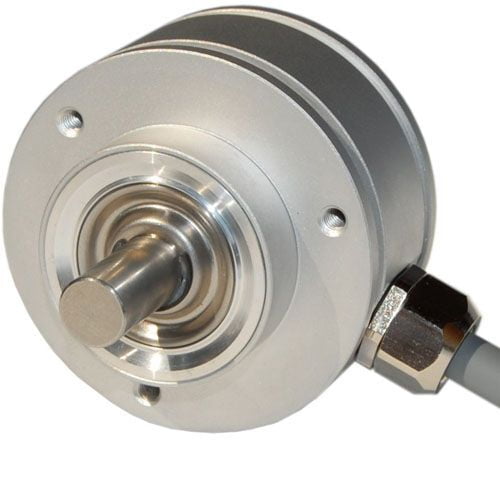
Acuro AR62 & AR63
The special features of the AR62/ 63 include not only a robust housing but also large dimensioned, block-type ball bearings. Even high axial and radial forces acting in the axial plane of the shaft of this rotary encoder will not cause it to miss a beat. The AR62/ 63 will cope with extreme acceleration, marked changes in climatic conditions and even work normally under water. This means it is predestined for use in wind turbines, ships and commercial vehicles just as much as in presses, wood-processing machines or stone masonry. In terms of its electrical design, the AR62 is compatible with standard industrial controller systems. The interfaces available are SSI, BiSS, CANopen and analogue. The encoder is available with resolutions from up to 12 bits as a single-turn unit and 16 bits as a multi-turn device.
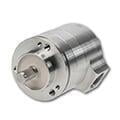
Acuro AX65
There are some encoder applications that are just demanding. Incredibly challenging. Among these are applications where the encoder has to be explosion-proof due to the dangerous atmosphere in which it operates. Or those that involve continual exposure to salt water. Or where it experiences huge shock loads of over 100 G. Or shaft loads of hundreds of Newtons. But the MOST demanding applications are those where the encoder must meet ALL these requirements. And that is exactly where the Hengstler AX65 comes in.
Certified explosion-proof, built with marine-grade stainless steel, with a shock rating of 200 G and shaft load of 300 N, the AX65 is one tough encoder. The most compact absolute encoder in its class, its shallow depth and body diameter of only 59 mm allow it to fit where other explosion-proof encoders can’t. The explosion-proof certification makes it ideal for offshore oil platforms, mines, chemical plants, etc., as does the marine grade stainless steel of which it’s built. The shaft load rating eliminates the need for load modules, reducing costs. The AX65 can be installed quickly and easily due to its flexible, quick-connect terminal system. Rounding out the AX65 is the choice of SSI or CANopen interface, which can save wiring costs by allowing a ring network configuration.
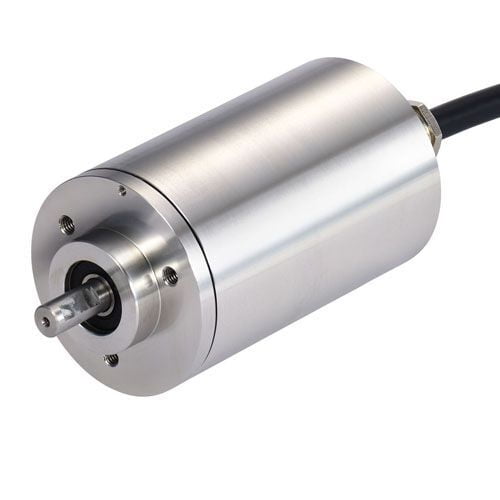
Acuro AX70 & AX71
Explosion-proof AX70 absolute encoders with an aluminium housing have been designed specifically for use in potentially explosive atmospheres. The pressure-resistant housing has been developed in compliance with the EN 60079 series of standards for use in explosive atmospheres and is permitted for use in environments where there is a risk of gas or dust explosion, zones 1 and 21. The encoders are available with a number of interfaces for use in various applications.
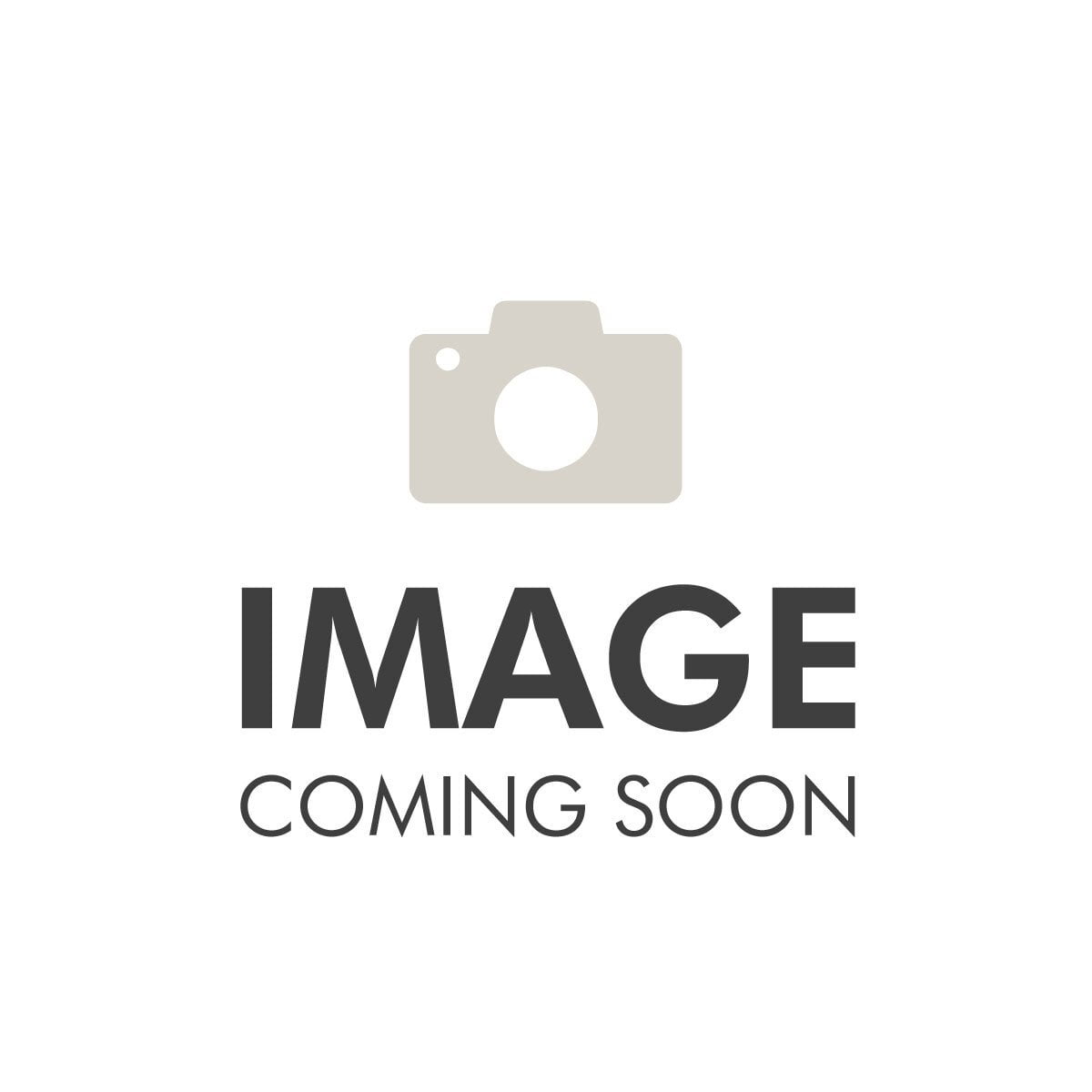
Acuro AX73
In the development of equipment for use in hazardous environments, selecting the right sensor plays a crucial role. First and foremost, explosion protection of the sensor itself is critical. Additional harsh requirements, such as the ability to withstand severe shock and vibration, and the need for corrosion resistance due to the working atmosphere, are placed on the encoder by the application itself. And, of course, an accurate and high-resolution sensor signal is required in spite of all other demands.
Hengstler has incorporated all these requirements into our new, explosion-proof, absolute encoder AX73 with interfaces SSI/BiSS or Profibus. With the addition of AX73, our explosion-proof product range is complete!
The optical scanning system of the AX73 encoder provides a highly accurate, high-resolution sensor signal that is also resistant to the strongest external magnetic fields.
The connection concept of the AX73 allows the routing of cabling and the final encoder installation to be done in separate steps. This provides significant cost and time savings during installation, as cabling can be done in advance. Emergency servicing can also be done more quickly, due to the ability to simply unplug the encoder cable and plug it into the replacement encoder.
With its ATEX and IECEx approvals, the Hengstler AX73 is certified and approved for international use, thus providing the user a global guarantee of safety and reliability in hazardous areas.